Ang katukma gigamit aron ipakita ang pagkamaayo sa produkto sa workpiece. Kini usa ka espesyal nga termino alang sa pagtimbang-timbang sa geometric nga mga parameter sa machining surface ug usa ka importante nga timailhan alang sa pagsukod sa performance sa CNC machining centers. Sa kinatibuk-an nga pagsulti, ang katukma sa machining gisukod sa grado sa pagtugot. Ang ubos nga grado, mas taas ang katukma. Ang pagliko, paggaling, pagplano, paggaling, pag-drill, ug paglaay mao ang kasagaran nga mga porma sa machining sa CNC machining centers. Busa unsa nga pagkasibu sa machining ang angay makab-ot niining mga proseso sa machining?
1.Pagliko tukma
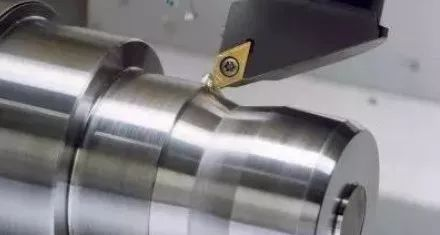
Ang pagliso nagtumong sa proseso sa pagputol diin ang workpiece nagtuyok ug ang himan sa pagliko nagalihok sa usa ka tul-id nga linya o kurba sa eroplano, nga gigamit sa pagproseso sa sulod ug gawas nga cylindrical nga mga ibabaw, mga nawong sa katapusan, mga conical ibabaw, pagporma sa mga ibabaw ug mga hilo sa workpiece.
Ang roughness sa nawong sa pagliko mao ang 1.6-0.8μm.
Ang mabangis nga pagliko nagkinahanglan sa paggamit sa dako nga pagputol sa giladmon ug dako nga feed rate aron sa pagpalambo sa turno efficiency nga walay pagkunhod sa cutting speed, ug ang ibabaw roughness kinahanglanon mao ang 20-10um.
Ang mga himan sa Xinfa CNC adunay mga kinaiya sa maayo nga kalidad ug ubos nga presyo. Para sa mga detalye, palihog bisitaha ang:CNC Tools Manufacturers - China CNC Tools Factory & Suppliers (xinfatools.com)
Ang semi-finishing ug finishing turning sulayi nga gamiton ang high speed ug gamay nga feed rate ug cutting depth, ug ang surface roughness mao ang 10-0.16um.
Ang pino nga gipasinaw nga himan sa pagbag-o sa diamante sa taas nga katukma nga lathe mahimo’g ibalik ang mga non-ferrous nga metal nga mga workpiece sa taas nga tulin, nga adunay usa ka kabangis sa nawong nga 0.04-0.01um. Kini nga matang sa pagliko gitawag usab nga "mirror turning".
2. Milling precision milling nagtumong sa paggamit sa rotating multi-blade tools sa pagputol sa mga workpiece, nga usa ka episyente kaayo nga pamaagi sa pagproseso.
Angayan alang sa pagproseso sa mga eroplano, grooves, ug nagkalain-laing splines, gears, thread molds ug uban pang espesyal nga mga ibabaw.
Ang roughness sa nawong sa paggaling kasagaran 6.3-1.6μm. Ang roughness sa nawong sa rough milling mao ang 5-20μm.
Ang roughness sa nawong sa semi-finishing milling mao ang 2.5-10μm. Ang roughness sa nawong sa maayong paggaling mao ang 0.63-5μm.
3. Pagkatukma sa pagplano
Ang pagplano usa ka pamaagi sa pagputol nga naggamit sa usa ka planer sa paghimo sa pinahigda nga relatibong linear reciprocating motion sa workpiece, kasagaran gigamit alang sa pagproseso sa porma sa mga bahin. Ang roughness sa nawong sa planing mao ang Ra6.3-1.6μm.
Ang roughness sa nawong sa rough planing mao ang 25-12.5μm. Ang roughness sa nawong sa semi-finishing planing mao ang 6.2-3.2μm. Ang roughness sa nawong sa maayong planing mao ang 3.2-1.6μm.
4. Pagkatukma sa paggaling Ang paggaling nagtumong sa pamaagi sa pagproseso sa paggamit sa mga abrasive ug mga galamiton sa paggaling aron maputol ang sobra nga materyal sa workpiece. Nahisakop kini sa maayong pagproseso ug kaylap nga gigamit sa industriya sa paghimo sa makinarya.
Ang paggaling kasagarang gigamit alang sa semi-finishing ug finishing, ug ang kabangis sa nawong kasagaran 1.25-0.16μm.
Ang roughness sa nawong sa precision grinding mao ang 0.16-0.04μm.
Ang roughness sa nawong sa ultra-precision grinding mao ang 0.04-0.01μm. Ang roughness sa nawong sa salamin grinding mahimong moabot ubos pa kay sa 0.01μm.
5. Makalaay
Kini usa ka proseso sa pagputol nga naggamit sa usa ka himan aron mapadako ang sulud sa sulud sa usa ka lungag o uban pang lingin nga contour. Ang sakup sa aplikasyon niini kasagaran gikan sa semi-roughing hangtod sa pagtapos. Ang himan nga gigamit kasagaran usa ka usa ka sulab nga boring tool (gitawag nga boring bar).
Ang makalaay nga katukma sa mga materyales nga asero kasagarang moabot sa 2.5-0.16μm.
Ang katukma sa pagproseso sa precision boring mahimong moabot sa 0.63-0.08μm.
Oras sa pag-post: Sep-03-2024